How Much Does A Paint Booth Cost
When it comes to industries that involve painting, having a paint booth is essential. A paint booth provides a controlled environment for painting operations, ensuring safety, quality, and compliance with regulations. If you’re considering investing in a paint booth, one of the crucial factors to consider is the cost. Understanding the expenses associated with a paint booth will help you make an informed decision and budget effectively for this important investment.
The cost of a paint booth can vary significantly depending on various factors such as size, type, ventilation systems, construction materials, and additional features. It’s important to assess your specific needs and requirements to determine the most suitable paint booth for your operations while considering the associated costs.
In this comprehensive guide, we will explore the factors that influence the cost of a paint booth, delve into different types of paint booths available, and provide insights into additional considerations that impact the overall expenses. By understanding the cost implications and conducting thorough research, you can make a well-informed decision that aligns with your budget and ensures a safe and efficient painting environment. So, let’s dive into the world of paint booths and discover how much they really cost.
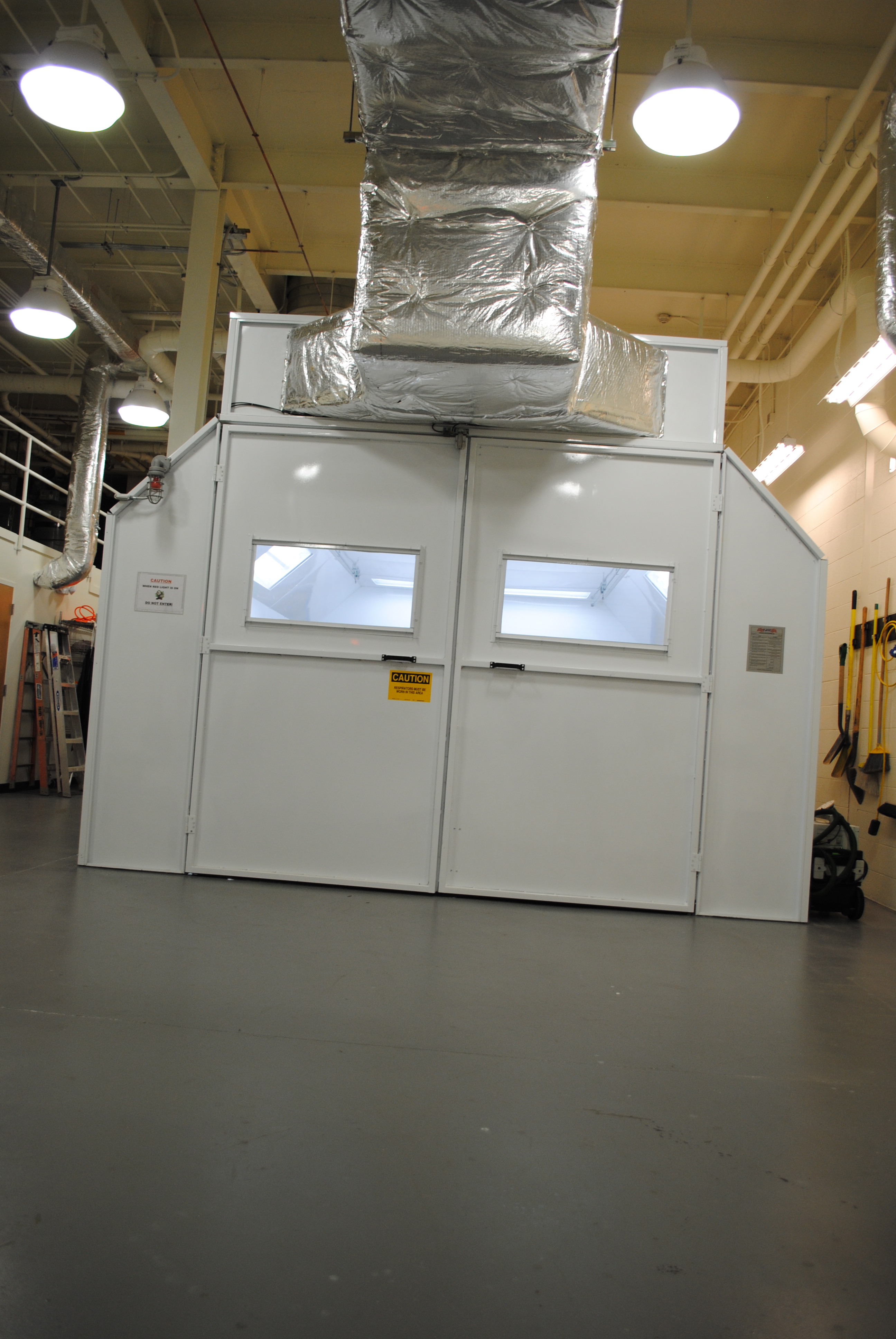
Understanding Paint Booths
A paint booth is a specialized enclosure designed to contain and control paint application processes. These booths are equipped with ventilation systems, filters, and other features to ensure the safe and efficient application of paint. Understanding the purpose and benefits of paint booths is essential before diving into the cost considerations.
Paint booths are necessary for several reasons:
- Safety and Health Regulations: Paint booths provide a controlled environment that helps prevent hazardous materials, such as paint fumes and overspray, from spreading throughout the workspace. By confining these materials within the booth, the risk of fire, explosions, and exposure to harmful chemicals is minimized.
- Environmental Considerations: Paint booths are designed to capture and filter harmful substances, preventing them from being released into the atmosphere. This helps maintain air quality and ensures compliance with environmental regulations regarding emissions.
- Improved Paint Application Quality: The controlled environment of a paint booth minimizes dust, debris, and other contaminants that can affect the quality of the paint job. It provides better lighting conditions, reducing the chances of uneven coating or missed spots.
Now that we have a clear understanding of the purpose and benefits of paint booths, let’s explore the different types available and their respective costs.
Types of Paint Booths
There are several types of paint booths available in the market, each designed for specific applications and requirements. Let’s take a closer look at the four primary types of paint booths:
Open-face Paint Booths
Open-face paint booths are the most basic and cost-effective option. They have three walls and an open front, allowing easy access to the booth. These booths rely on natural or ambient airflow for ventilation. While they provide basic protection, they are typically not suitable for highly regulated or precision painting processes.
Some key considerations regarding the cost of open-face paint booths include:
- Size and Dimensions: Larger booths will generally cost more due to increased material and construction requirements. Prices can vary based on the specific dimensions needed for your application.
- Ventilation and Airflow: Open-face booths rely on natural airflow, which may not be sufficient for certain painting operations. Additional ventilation systems may need to be installed, impacting the overall cost.
- Construction Materials: The materials used in constructing the booth, such as galvanized steel or powder-coated aluminum, can influence the cost. Different materials offer varying levels of durability and longevity.
Crossdraft Paint Booths
Crossdraft paint booths are designed with airflow that moves horizontally across the work area. They typically feature an exhaust fan at one end and intake filters on the opposite side. This airflow pattern helps remove overspray and contaminants from the workspace.
Consider the following factors when assessing the cost of crossdraft paint booths:
- Size and Dimensions: Larger booths will have higher material and construction costs. It’s important to determine the appropriate size based on your specific painting requirements.
- Ventilation and Airflow: Crossdraft booths rely on proper airflow management to maintain a clean work environment. Consider the cost of fans, filters, and other ventilation equipment when budgeting for a crossdraft booth.
- Construction Materials: The choice of construction materials affects the booth’s durability, maintenance requirements, and overall cost. Assess the pros and cons of different materials before making a decision.
Downdraft Paint Booths
Downdraft paint booths feature an airflow pattern that moves vertically from the ceiling down to the floor. This downward airflow helps capture overspray and contaminants efficiently. Downdraft booths are widely regarded as the gold standard for high-quality paint finishes.
When considering the cost of a downdraft paint booth, keep in mind the following aspects:
- Size and Dimensions: As with other booth types, larger downdraft booths will generally cost more due to increased material and construction requirements. Consider the size needed for your specific painting projects.
- Ventilation and Airflow: Downdraft booths require sophisticated ventilation systems to achieve proper airflow patterns. These systems may include intake filters, exhaust fans, and ceiling plenums. Factor in the cost of these components when budgeting for a downdraft booth.
- Construction Materials: Downdraft booths often utilize high-quality materials to ensure longevity and performance. Evaluate the costs associated with different construction materials, considering their durability and maintenance requirements.
Side-draft Paint Booths
Side-draft paint booths have an airflow pattern that moves horizontally from one end of the booth to the other. The intake filters are typically located on one side, and exhaust filters are located on the opposite side. Side-draft booths offer good paint finish quality and are commonly used in automotive refinishing.
Consider the following factors when assessing the cost of side-draft paint booths:
- Size and Dimensions: Larger side-draft booths will have higher material and construction costs. Consider the space requirements for your specific painting projects.
- Ventilation and Airflow: Side-draft booths rely on proper airflow management to achieve an even distribution of air. The cost of intake filters, exhaust fans, and other ventilation components should be considered.
- Construction Materials: The choice of construction materials impacts the booth’s durability and maintenance requirements. Evaluate the costs associated with different materials before making a decision.
Now that we have explored the different types of paint booths and their cost considerations, let’s delve into the factors that influence the overall cost of a paint booth.
Factors Influencing Paint Booth Costs
The cost of a paint booth can vary significantly depending on various factors. Understanding these factors will help you make an informed decision and budget effectively for your paint booth purchase. The following attributes play a crucial role in determining the overall cost:
Size and Dimensions
The size and dimensions of a paint booth are essential considerations that directly affect its cost. Larger booths require more materials for construction, additional ventilation systems, and potentially higher installation and setup costs. When determining the size of the paint booth you need, consider the specific requirements of your painting projects.
To give you an idea of the cost implications, here are some popular sizes and their approximate price ranges:
Size Range (ft) | Price Range ($) |
---|---|
10 x 10 | $5,000 – $10,000 |
20 x 15 | $10,000 – $20,000 |
30 x 20 | $20,000 – $30,000 |
Keep in mind that these price ranges are approximate and can vary based on factors such as construction materials and additional features.
Airflow and Ventilation Systems
Proper airflow and ventilation systems are critical for maintaining a clean and safe painting environment. The type and complexity of ventilation systems required for your paint booth can impact the overall cost. Consider the following aspects:
- Intake Filters: High-quality intake filters help ensure that only clean air enters the booth. The cost of these filters depends on their efficiency and lifespan.
- Exhaust Fans: The size and power of the exhaust fans needed to maintain proper airflow affect the cost. Larger booths or those with higher air exchange rates may require more powerful fans.
- Ductwork and Plenums: Depending on the layout and design of your paint booth, additional ductwork and plenums may be necessary. These components facilitate proper air distribution and filtration, contributing to the overall cost.
Construction Materials
The choice of construction materials for a paint booth can impact both the cost and the long-term durability of the booth. Common materials used include galvanized steel, powder-coated aluminum, and fiberglass reinforced plastic (FRP). Consider the following aspects when evaluating construction materials:
- Durability: High-quality materials may have a higher upfront cost but offer greater longevity and resistance to wear and tear. They can result in lower maintenance and replacement costs over time.
- Fire Resistance: Some materials have enhanced fire resistance properties, which can be beneficial for safety compliance. However, they may come at a higher cost.
- Maintenance Requirements: Different materials have varying maintenance needs. Evaluate the long-term costs associated with cleaning, repairs, and replacements when selecting construction materials.
Filtration Systems
Filtration systems are crucial components of paint booths, helping to capture overspray and contaminants. The cost of filtration systems depends on the type and quality of filters used. Common types of filters include:
- Exhaust Filters: These filters capture overspray particles and prevent them from being released into the environment. Higher quality filters may have a higher initial cost but provide better filtration efficiency.
- Intake Filters: Intake filters help ensure that only clean air enters the booth. The cost of these filters can vary based on their efficiency and lifespan.
Consider the filtration requirements of your specific painting processes and evaluate the costs associated with different filter options.
Lighting and Electrical Systems
Adequate lighting is essential for accurate color matching, identifying imperfections, and ensuring overall painting quality. The lighting requirements for a paint booth can influence the cost. Consider the following aspects:
- Lighting Fixtures: High-quality lighting fixtures designed for paint booths may have a higher upfront cost. However, they offer better color rendering and durability, resulting in improved paint application quality.
- Energy Efficiency: Energy-efficient lighting options, such as LED fixtures, can help reduce long-term operating costs by minimizing energy consumption. Although they may have a higher initial cost, they can provide cost savings over the lifespan of the booth.
Evaluate the specific lighting needs of your painting operations and balance upfront costs with long-term energy savings.
Control Panels and Automation
Control panels and automation features can enhance the efficiency and convenience of operating a paint booth. While they may add to the overall cost, they can also provide benefits such as improved process control and reduced manual labor. Consider the following aspects:
- Control Panels: Advanced control panels allow for precise adjustment of airflow, temperature, and other parameters. The complexity and capabilities of the control panel can affect the cost.
- Automation Features: Automation features such as programmable timers, remote control, and automatic shutdown systems can streamline painting operations. These features may come at an additional cost but can contribute to increased efficiency and productivity.
Evaluate the potential benefits and long-term cost savings that automation features can offer for your specific painting processes.
Additional Considerations
When budgeting for a paint booth, it’s important to consider several additional factors that can impact the overall cost and long-term operation. Let’s explore these considerations in more detail:
Installation and Setup Costs
The installation and setup of a paint booth require careful planning and professional expertise. While it’s possible to opt for a do-it-yourself (DIY) approach, hiring professionals is often recommended to ensure proper installation and compliance with regulations. Consider the following aspects when assessing installation and setup costs:
- Professional Installation: Hiring experienced technicians to install the paint booth can ensure that it is set up correctly and in compliance with safety and regulatory standards. The cost of professional installation may vary depending on factors such as booth size and complexity.
- Site Preparation: Adequate site preparation is crucial for a successful paint booth installation. This may include tasks such as leveling the floor, providing proper electrical connections, and ensuring sufficient space around the booth for maintenance and access. Site preparation costs should be factored into the overall budget.
While professional installation can add to the upfront costs, it provides peace of mind and ensures a smooth setup process.
Maintenance and Operational Costs
Maintaining and operating a paint booth involves ongoing costs that should be considered when budgeting. Proper maintenance is essential for ensuring optimal performance, longevity, and compliance with safety standards. Some key factors to consider include:
- Regular Maintenance: Paint booths require routine maintenance tasks such as filter replacements, cleaning, and equipment inspections. The cost of maintenance will vary depending on the size and complexity of the booth, as well as the frequency of required tasks.
- Spare Parts and Repairs: It’s important to account for potential repair costs and the availability of spare parts for the paint booth. Research the availability and pricing of spare parts specific to the model and brand of your booth.
- Energy Consumption: Paint booths can consume a significant amount of energy, especially if they are equipped with powerful ventilation systems and lighting fixtures. Consider the potential energy costs and explore energy-efficient options to minimize long-term operational expenses.
By incorporating maintenance and operational costs into your budget, you can ensure the proper functioning and longevity of your paint booth.
Compliance and Permits
Compliance with safety and environmental regulations is essential when operating a paint booth. Depending on your location and specific industry, certain permits or certifications may be required. Consider the following aspects:
- Regulatory Requirements: Research and understand the local, state, and federal regulations that apply to your industry and the operation of a paint booth. This may include requirements related to air quality, emissions, and waste disposal. Compliance with these regulations may involve additional costs, such as inspections and permit fees.
- Permitting Process: Determine the specific permits and certifications needed for your paint booth. This may include obtaining permits for installation, operation, and potentially hazardous materials storage. Budget for any fees associated with the permitting process.
Compliance with regulations not only ensures a safe working environment but also avoids potential fines or penalties.
Budgeting for a Paint Booth
Now that we have explored the various factors that influence the cost of a paint booth, it’s time to delve into the process of budgeting effectively. Consider the following steps to help you make informed decisions and stay within your financial means:
Researching and Gathering Information
Start by researching paint booth suppliers, manufacturers, and industry resources. Explore online platforms, industry publications, and forums to gather information on different types of paint booths, prices, and customer reviews. Engage with industry experts and seek their advice to gain valuable insights.
Assessing Specific Needs and Requirements
Evaluate your specific needs and requirements for a paint booth. Consider factors such as the size of the objects being painted, the types of coatings used, and any specialized features or functionalities you may require. By identifying your specific needs, you can narrow down the options and focus on paint booths that best align with your requirements.
Requesting Quotes and Comparing Options
Contact multiple paint booth suppliers and request detailed quotes based on your specific needs. Compare the offerings, pricing, and included features of different suppliers. It’s essential to consider the overall value and quality of the booth rather than solely focusing on the initial cost. Take into account factors such as construction materials, ventilation systems, warranty, and customer support.
Evaluating the Value for the Cost
When evaluating the cost of a paint booth, it’s crucial to consider the long-term value it provides. A higher initial investment in a well-built, efficient booth can result in cost savings over time through improved productivity, reduced energy consumption, and fewer maintenance requirements. Assess the value proposition of each option and make an informed decision that aligns with your budget and specific requirements.
Case Studies and Examples
To gain a better understanding of the costs associated with paint booths, let’s explore some real-world case studies and examples. These examples highlight different industries, booth sizes, and specific cost breakdowns, providing practical insights into the investment required.
Case Study 1: Automotive Refinishing Shop
In an automotive refinishing shop, a medium-sized downdraft paint booth was installed to accommodate the painting of cars, trucks, and motorcycles. Here’s a breakdown of the costs involved:
- Booth Size: 25 x 15 feet
- Construction Materials: Powder-coated steel
- Ventilation System: High-efficiency exhaust fans and intake filters
- Lighting: Energy-efficient LED fixtures
- Control Panel: Advanced control panel with programmable timers
Total Cost: $35,000 (including professional installation)
The investment in a high-quality booth ensured precise paint application, excellent airflow control, and compliance with safety regulations. The shop experienced improved paint finish quality, reduced overspray, and increased customer satisfaction.
Case Study 2: Industrial Manufacturing Facility
In an industrial manufacturing facility, an open-face paint booth was installed to handle the painting of large machinery and equipment. Here’s a breakdown of the costs involved:
- Booth Size: 40 x 30 feet
- Construction Materials: Galvanized steel
- Ventilation System: Natural airflow with additional exhaust fans
- Lighting: Standard fluorescent fixtures
- Control Panel: Basic manual controls
Total Cost: $20,000 (including professional installation)
While the open-face booth provided a cost-effective solution, it required additional ventilation upgrades to ensure proper airflow control. The booth successfully met the facility’s painting needs, but with some limitations in terms of overspray control and environmental compliance.
Conclusion
Investing in a paint booth is a significant decision that requires careful consideration of various factors, including cost. By understanding the different types of paint booths, the factors that influence their costs, and the additional considerations involved, you can make an informed decision that aligns with your budget and specific requirements.
Remember to assess the size, ventilation systems, construction materials, filtration systems, lighting, and control panels when evaluating costs. Additionally, consider the installation and setup costs, ongoing maintenance and operational expenses, and any compliance and permit requirements.
By budgeting effectively and choosing a paint booth that offers the best value for your investment, you can create a safe, efficient, and high-quality painting environment that meets your business needs.